Working principle of laser cutting machine
Laser is a laser emitted from the laser, through the optical path system, focused into a high power density laser beam.The laser beam hits the surface of the workpiece to reach the melting or boiling point, and high-pressure gas coaxial with the laser beam blows away the melted or evaporated metal.When the beam moves relative to the workpiece, the material eventually forms a slit, thus achieving the purpose of cutting.
Laser cutting metal is to replace the traditional mechanical knife and invisible beam, high precision, fast cutting, not limited to cutting patterns, automatic typesetting save material, smooth incision, low processing cost characteristics, no mechanical stress incision, shear burr;High machining precision, good repeatability, do not destroy the material surface, NUMERICAL control programming, can deal with any plane, can be a large format whole board cutting, no mold opening, economical and time-saving.
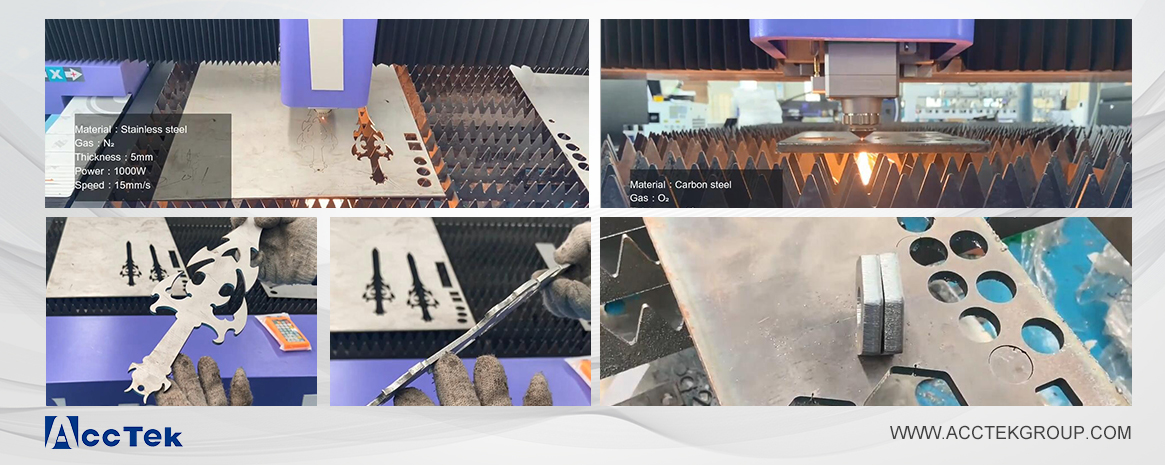
Laser cutting technology classification
Laser cutting can be divided into laser vaporization cutting, laser melting cutting, laser oxygen cutting and laser cutting and control fracture four categories.The following is a detailed analysis of various cutting processes:
1) Laser vaporization cutting
Using high energy density laser beam to heat the workpiece, the workpiece temperature rises rapidly, in a very short time to reach the boiling point of the material.The matter begins to vaporize, forming steam.The steam shot out at such a high speed that it made a cut in the material.The heat of vaporization of materials is generally very large, so laser vaporization cutting requires a large power and power density.Laser vaporization cutting is mainly used for cutting extremely thin metal materials and non-metallic materials.
2) Laser melting
In the process of laser melting and cutting, the metal material is melted by laser heating, and then non-oxidizing gas (Ar, He, N, etc.) is ejected through the nozzle coaxial with the beam, and the liquid metal is discharged under the strong pressure of the gas to form an incision.Laser melting and cutting does not require complete vaporization of the metal, but only 1/10 of the energy of vaporization of the cutting.Laser fusion cutting is mainly used for the cutting of some non-oxidizing materials or active metals, such as stainless steel, titanium, aluminum and their alloys.
3) Laser oxygen cutting
Principle of laser oxygen cutting is similar to oxyacetylene cutting.It USES laser as the preheating heat source, oxygen and other active gases as cutting gas.On the one hand, the ejected gas interacts with the cutting metal, producing an oxidation reaction that releases a large amount of oxidizing heat.On the other hand, molten oxide and molten material are blown out of the reaction zone, creating incisions in the metal.Because the oxidation reaction produces a lot of heat in the cutting process, the energy required by laser oxygen cutting is only 1/2 of that required by melting cutting, and the cutting speed is far greater than that of laser vaporization cutting and melting cutting.Laser oxygen cutting is mainly used for carbon steel, titanium steel, heat treatment steel and other easily oxidized metal materials.
4) Laser scanning and controlling fracture
Laser scanning is used to scan the surface of brittle material with high energy density laser, which makes the material evaporate into groove after heating.A certain amount of pressure is then applied and the brittle material will crack along the slit.Q - switched laser and CO2 laser are generally used for laser marking.Fracture control is to make use of the steep temperature distribution generated by laser grooving to generate local thermal stress in brittle materials so that the materials fracture along the grooving.
Advantages of laser cutting metal
Laser cutting metal craftsmanship is an advanced technique used in many metal fabrication projects. Manufacturers use many different methods to cut metal, but laser cutting is one of the most advanced. Manufacturers often choose fiber laser cutting machine for their ability to make precise cuts at speeds unmatched by other flatbed cutting methods. Read below to learn about the benefits of cutting metal with a fiber laser cutter.
1. Faster cutting speed for increased workshop productivity
Laser cutting is known for its ability to cut metal quickly and accurately, at a very fast rate. When cutting thick metal, the cutting time is extended, but they still work very fast compared to traditional metal cutting methods. Fiber laser cutters are ideal for small and large operations and can help reduce production time by reducing the time it takes to cut material. When manufacturers use the right type of laser cutter, they can provide the fastest cutting speeds on the market. This makes it possible for companies to expand their business scope. In addition to fast cutting times, laser cutters increase manufacturing efficiency because multiple parts can be programmed and cut at once.
2. Higher cutting accuracy, improve workpiece quality
Laser cutters are virtually unmatched in precision, producing clean edges and smooth surfaces. Anything in the laser's path will burn, vaporize, or melt. So, there won't be any excess chips to cause a rough cut. This cutting precision not only produces high-quality parts, but also helps reduce raw material waste during production. Because laser cutters can produce such high-precision parts, they are an excellent choice for cutting parts used to make aerospace parts and medical devices that require tight dimensional tolerances and quality standards.
3. More energy saving and environmental protection
The efficiency of a fiber laser cutter combined with its advanced technology allows it to use less energy than other cutting methods. As metal manufacturers look to work smarter and use less energy, whether as a cost-saving mechanism or an environmentally friendly mechanism, laser cutters can help make that happen. Laser cutters are a great way to reduce energy use in the manufacturing process.
4. Laser-cut finished products have higher consistency
Because laser cutters can make such precise cuts, you can be sure your parts and assemblies are accurate. Laser cutters are programmed with a CNC CAD/CAM program, ensuring that the same cut can be repeated as many times as needed. Because laser cutting is so precise, you can be sure that the cut is exactly as programmed. The result of this precision and programming is consistency for every manufacturing item. When creating multiple copies of the same product, you can be sure that each copy will have the exact same results. You can also be sure that every time you use your laser cutter, it will produce the same quality product.
5. Versatility for cutting sheet metal and metal pipes
The fiber laser cutting machine can cut both metal sheets and metal pipes by adding a rotating shaft device. It can cut all different types and thicknesses of material, helping metal fabricators with a variety of projects. With a professional CNC cutting system, laser metal cutting machines can easily cut simple and complex structures and simultaneously process all these materials (even different materials) into complex and highly precise shapes. Their precision and accuracy mean that the types of cuts that laser cutters are capable of are virtually endless.
6. No damage to cutting, reducing finishing requirements
The tight focus of the laser beam means no internal defects due to heat. So the laser cutting machine will produce high quality, precise cuts and quality checks will take less time. They ensure that all part specifications are met, allowing for effective quality checks. Since laser cutters produce high-precision cuts, they will reduce the necessary finishing requirements.
The main reason for using laser cutting technology is to reduce the mechanical stress that the metal sheet is subjected to when it is cut. Not only does the laser eliminate impact stress that can adversely affect sheet metal products during the cutting process, but the heated area is very small. This means that the rest of the workpiece has little or no exposure to heat, thus maintaining the properties of the material being processed. Plus, because laser cuts can be made very close to each other without negatively impacting the sheet metal, they help minimize waste—tighter cuts allow you to make more per square foot of sheet metal used parts.
As a laser cutting machine manufacturer, ACCTEK provides users with professional laser cutting equipment. Including fiber laser cutting machines for cutting metals and CO2 laser cutting machines for processing non-metals. In addition to high-quality machines, we also provide users with free technical support. When you receive the machine, our laser machine engineers will provide online training and troubleshooting services, allowing you to become an experienced laser cutting machine operator faster.
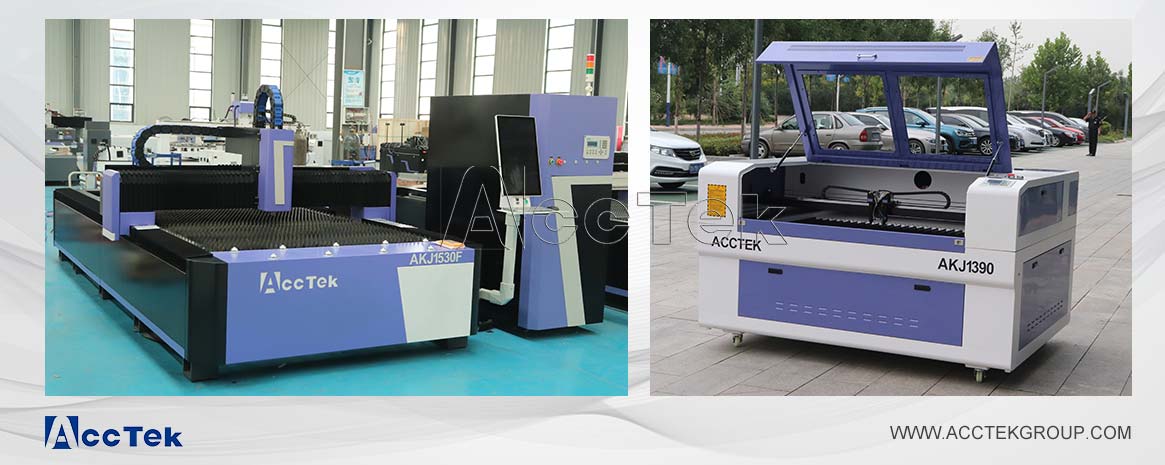
Fiber laser cutting machine and CO2 laser cutting machine