
What Are The Hazards of Laser Welding?
This article explores the various hazards of laser welding, including radiation, fumes, electrical risks, and safety standards, with detailed insights and prevention strategies.

Pulse VS Continuous Laser Cleaning Machines
This article compares pulse and continuous laser cleaning machines, detailing their working principles, key features, applications, advantages, and selection criteria.

Understanding The Operating Costs of Laser Cutting Machines
This article explains the key factors that influence the operating costs of fiber and CO2 laser cutting machines, including energy, maintenance, labor, and material efficiency.

How to Maintain the Oscillating Knife Cutting Machine?
This article provides a comprehensive guide to maintaining an oscillating knife cutting machine, covering daily care, troubleshooting, servicing, and best practices.

What Are The Risks of Using CNC Routers?
This article explores the various risks associated with using CNC routers, including mechanical, electrical, environmental, and human factors, along with ways to mitigate them.

What Materials Can Be Effectively Marked Using Laser Marking?
This article explores the types of materials that can be effectively marked using laser technology, including metals, plastics, ceramics, glass, and composites.

What Materials Can Be Welded With Lasers?
This article explores the wide range of materials that can be welded using lasers, covering metals, non-metals, composites, and key factors that affect weldability.

What Are The Advantages and Disadvantages of Laser Cleaning?
This article explores the key advantages and disadvantages of laser cleaning technology, including its applications, limitations, and how it compares to traditional methods.
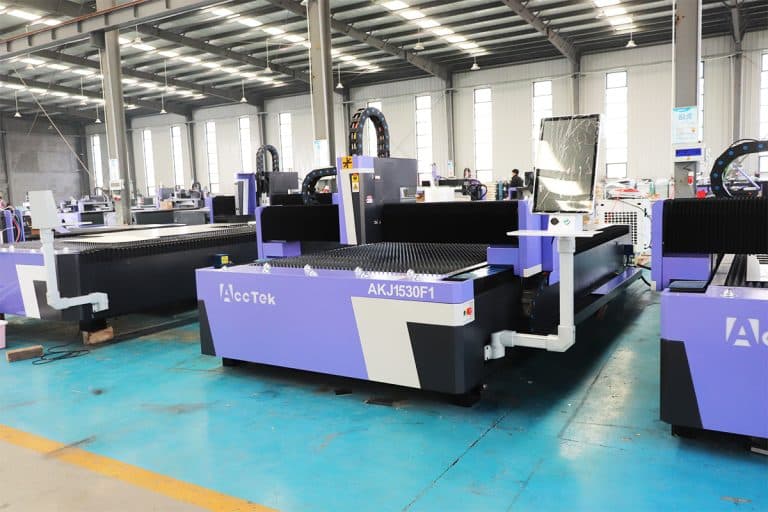
Laser Cutting VS Waterjet Cutting
This article compares laser cutting and waterjet cutting technologies, examining their principles, applications, costs, advantages, and key considerations for choosing between them.
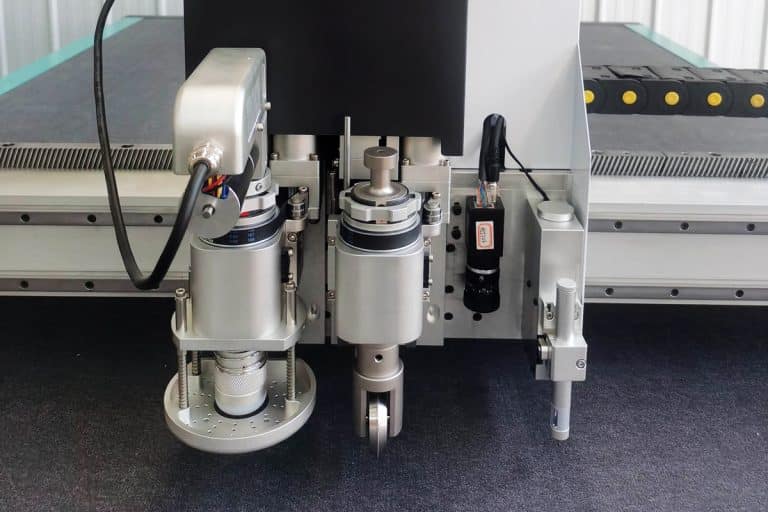
What to Consider Before Buying Oscillating Knife Cutting Machines
This article outlines key factors to consider when buying oscillating knife cutting machines, including performance, materials, software, safety, and vendor selection.

What Are The Hazards of Laser Welding?
This article explores the various hazards of laser welding, including radiation, fumes, electrical risks, and safety standards, with detailed insights and prevention strategies.

Pulse VS Continuous Laser Cleaning Machines
This article compares pulse and continuous laser cleaning machines, detailing their working principles, key features, applications, advantages, and selection criteria.

Understanding The Operating Costs of Laser Cutting Machines
This article explains the key factors that influence the operating costs of fiber and CO2 laser cutting machines, including energy, maintenance, labor, and material efficiency.

How to Maintain the Oscillating Knife Cutting Machine?
This article provides a comprehensive guide to maintaining an oscillating knife cutting machine, covering daily care, troubleshooting, servicing, and best practices.

What Are The Risks of Using CNC Routers?
This article explores the various risks associated with using CNC routers, including mechanical, electrical, environmental, and human factors, along with ways to mitigate them.

What Materials Can Be Effectively Marked Using Laser Marking?
This article explores the types of materials that can be effectively marked using laser technology, including metals, plastics, ceramics, glass, and composites.

What Materials Can Be Welded With Lasers?
This article explores the wide range of materials that can be welded using lasers, covering metals, non-metals, composites, and key factors that affect weldability.

What Are The Advantages and Disadvantages of Laser Cleaning?
This article explores the key advantages and disadvantages of laser cleaning technology, including its applications, limitations, and how it compares to traditional methods.

Laser Cutting VS Waterjet Cutting
This article compares laser cutting and waterjet cutting technologies, examining their principles, applications, costs, advantages, and key considerations for choosing between them.

What to Consider Before Buying Oscillating Knife Cutting Machines
This article outlines key factors to consider when buying oscillating knife cutting machines, including performance, materials, software, safety, and vendor selection.