Product Introduction
Types of 3 Axis CNC Routers
-
AKM1325 CNC Router
Rated 4.75 out of 5$4,300.00 This product has multiple variants. The options may be chosen on the product page -
AKM1530 CNC Router
Rated 4.50 out of 5$4,900.00 This product has multiple variants. The options may be chosen on the product page -
AKM2030 CNC Router
Rated 5.00 out of 5$5,500.00 This product has multiple variants. The options may be chosen on the product page -
AKM2040 CNC Router
Rated 4.75 out of 5$6,000.00 This product has multiple variants. The options may be chosen on the product page -
AKM-C1 CNC Router
Rated 5.00 out of 5$9,800.00 – $11,400.00Price range: $9,800.00 through $11,400.00 This product has multiple variants. The options may be chosen on the product page -
AKM-C2 CNC Router
Rated 4.50 out of 5$12,700.00 – $14,300.00Price range: $12,700.00 through $14,300.00 This product has multiple variants. The options may be chosen on the product page -
AKM-C3 CNC Router
Rated 4.50 out of 5$17,400.00 – $19,000.00Price range: $17,400.00 through $19,000.00 This product has multiple variants. The options may be chosen on the product page -
AKM1325C CNC Router
Rated 4.75 out of 5$9,800.00 – $17,400.00Price range: $9,800.00 through $17,400.00 This product has multiple variants. The options may be chosen on the product page
Application of 3 Axis CNC Routers
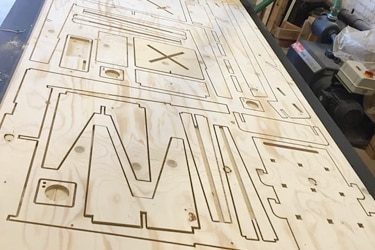
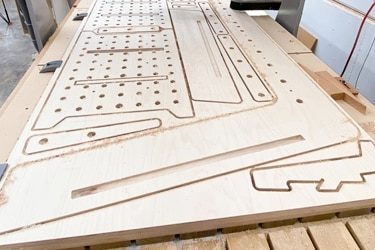
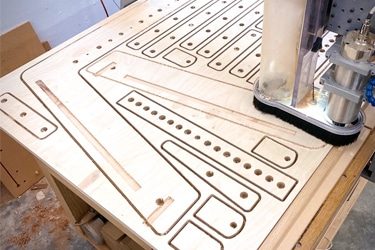
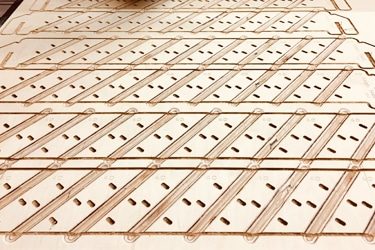
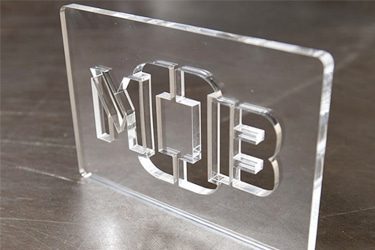
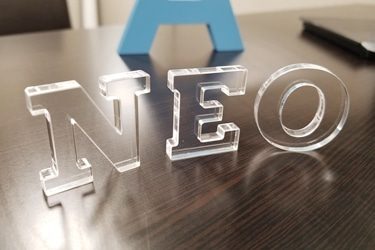
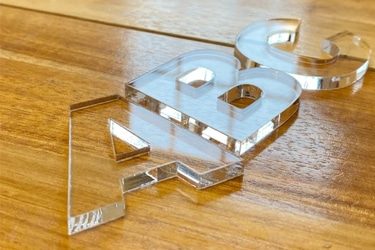
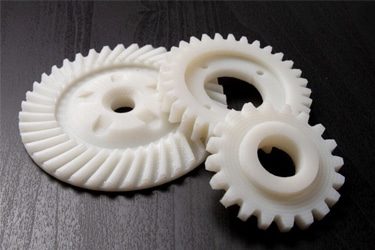
Customer Testimonials
3 Axis CNC Routers VS Other Engraving Machines
Comparison Item | 3 Axis CNC Router | Laser Engraving Machine | CNC Milling Center | CNC Lathe |
---|---|---|---|---|
Cutting Method | Rotary cutting with a spindle and bits | Focused laser beam | Precision cutting with rigid tools | Cutting by rotating the workpiece |
Axes of Movement | 3 axes (X, Y, Z) | Typically 2 axes | 3 to 5 axes | 2 axes (X, Z) |
Material Compatibility | Wood, plastic, foam, soft metals | Non-metals, coated metals | Metals, plastics, and composites | Round metals, rigid plastics |
Best For | Flat and shallow 3D carving | Surface marking and fine engraving | High-precision machining | Cylindrical and symmetrical parts |
Surface Finish Quality | Good (depends on tooling) | Excellent | Excellent | Excellent |
Cutting Depth Capability | Moderate | Shallow (marking only) | High | High |
Precision | High (±0.1 mm) | Very high (±0.01 mm) | Very high (±0.01 mm) | High |
Complexity of Shapes | 2D + shallow 3D designs | Mostly 2D surface details | Complex 3D profiles | Rotational symmetry only |
Cutting Speed | Fast on soft materials | Very fast on thin materials | Slower due to precision | Fast for round parts |
Tool Wear | Moderate, depends on the material | None (non-contact) | High (especially for hard metals) | Moderate |
Maintenance Requirements | Low | Low | High | Medium |
Operating Cost | Low to moderate | Low | High | Moderate |
Setup Complexity | Easy to moderate | Easy | Complex | Moderate |
Automation Compatibility | High (CNC-based) | High | High | High |
Ideal Industries | Woodworking, signage, and plastics | Electronics, crafts, and packaging | Aerospace, molds, metal parts | Automotive, hardware, shafts |
Why Choose Us
High Precision & Efficiency
AccTek CNC routers deliver fast, accurate results with minimal errors, supporting intricate designs and mass production across the woodworking, plastic, and metal industries.
Robust and Durable Design
Our machines are built with high-quality frames and components, ensuring long service life, high load-bearing capacity, and stability during high-speed operations.
Intelligent Control Systems
Equipped with user-friendly interfaces and smart controllers, our routers offer smooth motion control, automatic toolpath optimization, and easy integration with various CAD/CAM software.
Flexible Customization
From machine size to spindle power and motor type, we offer flexible configurations to suit different production needs, budgets, and material requirements.
Related Resources

What Are The Risks of Using CNC Routers?
This article explores the various risks associated with using CNC routers, including mechanical, electrical, environmental, and human factors, along with ways to mitigate them.
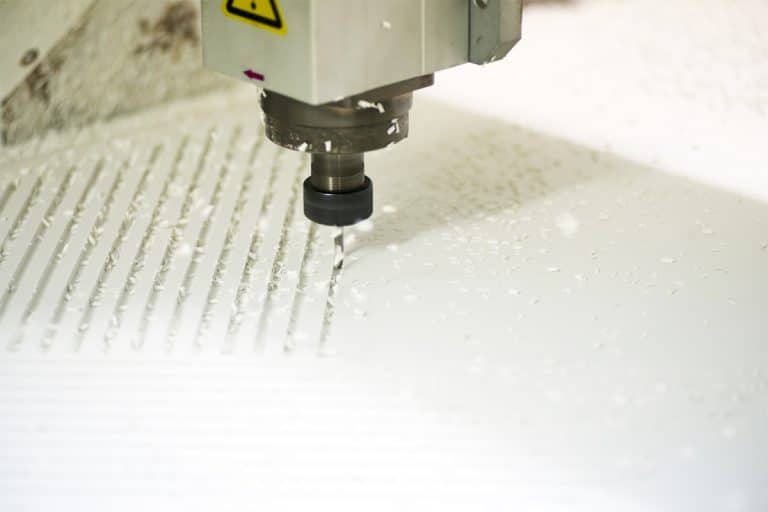
What Are 4-Axis CNC Routers?
This article explains what 4-axis CNC routers are, how the swing-head A-axis works, and what advantages, applications, and considerations come with this advanced technology.
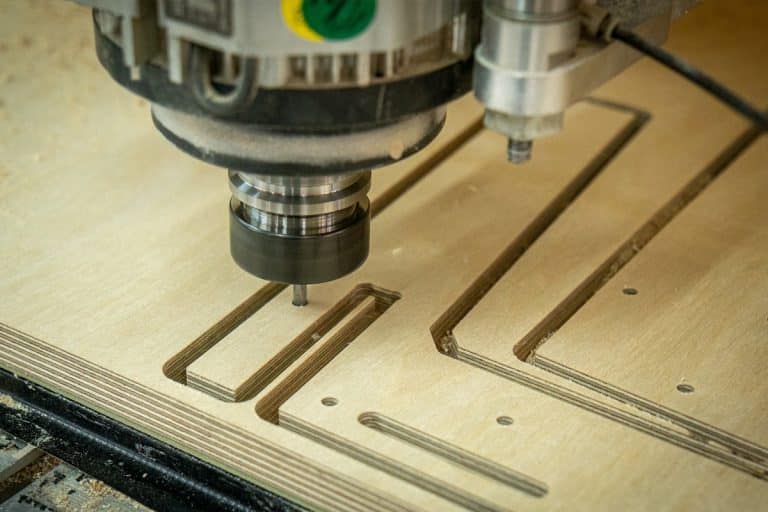
What Are 3-Axis CNC Routers?
This article explains what 3-axis CNC routers are, how they work, their key components, typical applications, benefits, limitations, and how to choose the right machine.
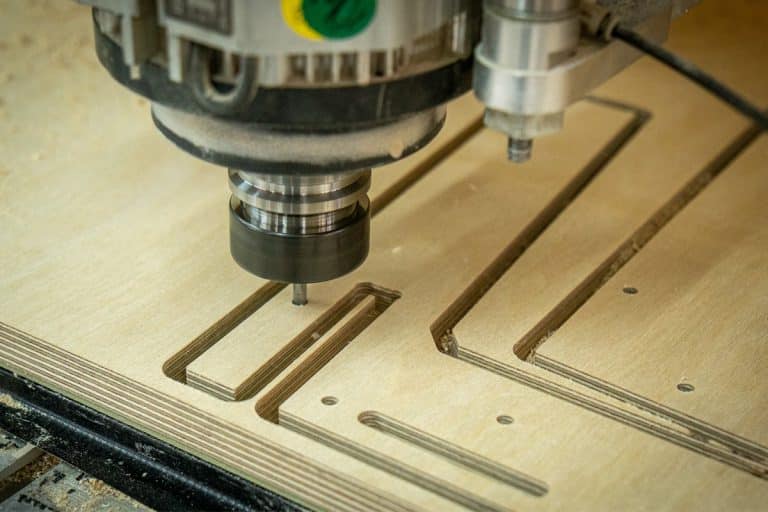
What Is CNC Routing?
Discover the fundamentals of CNC routing, its applications, advantages, challenges, and how advanced CNC technology enhances precision and efficiency across industries.
Frequently Asked Questions
What Can 3-Axis CNC Routers Do?
- Cutting and Profiling: Shape the outer edge of a part from materials like wood, plastic, or soft metals. Great for signs, panels, and parts that need clean, accurate edges.
- Pocketing and Grooving: Remove material from inside a part to create pockets, slots, or grooves. Common in cabinetry, mold-making, and packaging designs.
- Engraving and Etching: Engrave text, logos, or designs into flat surfaces. Useful for signage, nameplates, and decorative work.
- Drilling and Boring: Drill accurate holes in consistent locations—ideal for joinery, hardware mounting, or assembly alignment.
- Relief Carving: Create 2.5D (two-and-a-half-dimensional) carvings, where depth varies slightly to give a 3D appearance. Used for art, signs, and wood panels.
- Template and Jig Making: Produce repeatable, precision templates and jigs to streamline other workshop operations.
- Small Batch Production: Efficiently produce multiple identical parts with tight tolerances, great for small businesses or prototyping.
While 3-axis CNC routers can’t machine undercuts or full 3D shapes from all angles, they’re highly capable for flat and moderately contoured work, offering precision, repeatability, and efficiency for a wide variety of tasks.
What Materials Can 3-Axis CNC Routers Process?
- Wood: Handles softwoods, hardwoods, plywood, MDF, and particle board with ease. Ideal for furniture, cabinetry, signs, and decorative panels.
- Plastics: Processes acrylic, PVC, polycarbonate, HDPE, and similar materials. Useful in prototyping, enclosures, and display manufacturing.
- Foam: Cuts EVA, rigid foam, and polyurethane foam cleanly—great for packaging, props, and insulation.
- Soft Metals (Limited): Aluminum, brass, and copper can be machined with a rigid 3-axis CNC router, sharp bits, and proper feeds and speeds. However, metal removal is slower and less efficient than on a CNC mill.
- Stone (Limited): Some 3-axis CNC routers, especially heavy-duty or water-cooled models, can cut soft stone like marble, slate, or engineered stone. This requires the right tooling (diamond bits) and water or air cooling to prevent overheating.
- Composites: Handles fiberglass, carbon fiber, and laminates with appropriate tooling and dust control systems.
While 3-axis CNC routers can remove metal and stone, they are not optimized for it. The machine must be rigid, use appropriate bits, and run with reduced cutting speeds. In short, 3-axis CNC routers are versatile across many materials—but when it comes to metal and stone, they’re best for light-duty, low-volume tasks.
How Do I Choose 3-axis CNC Routers?
- Material Compatibility
- Make sure the CNC router can handle your primary materials.
- For wood, plastics, and foam, most standard CNC routers work fine.
- For aluminum or composites, you’ll need a stronger frame and higher spindle power.
- Occasional stone or metal cutting? Look for industrial-grade models with cooling systems and proper tooling support.
- Spindle Power
- Spindle strength impacts cut depth, speed, and material range.
- 5kW–2.2kW: Light-duty use—good for signs, hobby work.
- 0kW–4.5kW: Mid-range—handles hardwood, MDF, soft metals.
- 5kW+: Heavy-duty—suitable for continuous use and denser materials.
- Work Area Size
- Pick a table size that matches your typical project.
- Common sizes: 600×900mm, 1300×2500mm, 1500×3000mm.
- Larger beds offer more flexibility but cost more and require more space.
- Frame and Rigidity
- A solid frame reduces vibration and improves accuracy.
- Prefer steel or heavy-duty aluminum builds.
- Avoid lightweight or flimsy frames for precision work.
- Drive System
- Ball screw drives: High precision, better for small, detailed work.
- Rack and pinion: Faster, better for large-format projects.
- Controller and Software
- Choose a machine with reliable control hardware and G-code compatibility.
- Look for DSP, Mach3, or RichAuto controllers.
- Ensure it works with common design software like Fusion 360, VCarve, or Aspire.
- Dust Collection
- Essential for clean operation—especially in wood or composite shops.
- Look for a dust shoe and proper ports for connecting a vacuum system.
- Customer Support and Warranty
- Good support saves time and money. Go with a brand that offers:
- Detailed manuals and videos
- Prompt tech support
- Easy access to replacement parts
Match the CNC router to your materials, job size, and workload. Don’t just chase specs—prioritize build quality, spindle power, and post-sale support.
How Much Do 3-Axis CNC Routers Cost?
- Consumer-Grade 3-Axis CNC Routers ($3,500–$4,000): These are entry-level machines designed for hobbyists, small workshops, or light-duty use. They typically have smaller work areas, lower spindle power (1.5kW–2.2kW), and basic controllers. Suitable for cutting wood, plastic, and foam with moderate accuracy.
- Industrial-Grade 3-Axis CNC Routers ($4,500–$7,000): Built for durability and precision, these routers come with stronger frames, larger work areas, and higher spindle power (3.0kW–4.5kW). They can handle hardwoods, composites, and even light aluminum, making them ideal for professional shops and production environments.
The price you pay should reflect your production needs. For basic projects or occasional use, a consumer-grade machine works fine. For consistent accuracy, larger jobs, or tougher materials, the investment in an industrial-grade model pays off in speed, reliability, and cut quality.
What Are The Disadvantages Of 3-axis CNC Routers?
- Limited to Simple Geometries: They can only move along the X, Y, and Z axes, so they can’t machine complex undercuts, deep cavities, or full 3D surfaces from multiple angles.
- Single-Side Machining: To machine multiple sides of a part, you have to manually flip or reposition it, which increases setup time and risks alignment errors.
- Slower for Complex Jobs: 3-axis CNC routers take longer to machine intricate parts that would be faster and easier on a 4- or 5-axis machine.
- Material Access Limitations: They can’t reach around or underneath features, which limits their use for molds, aerospace parts, or detailed sculptures.
- Less Efficient for High-Volume or Multi-Tool Work: Without an automatic tool changer (unless custom added), every tool swap must be done manually, slowing down production.
- Not Ideal for Heavy Metal or Stone Work: Most 3-axis CNC routers aren’t rigid enough for prolonged cutting of dense materials like steel or granite. They’re better suited for wood, plastic, foam, and soft metals like aluminum.
3-axis CNC routers are great for flat parts, 2.5D work, and simple production runs—but they fall short when it comes to multi-sided machining, complex 3D parts, and higher-volume industrial jobs.
What Spindle Power Options Are Available For 3-Axis CNC Routers?
- 1.5kW: Light-duty use. Best for engraving, signs, and small woodworking projects using softwood, plastic, or foam.
- 2.2kW: Entry-level spindle for light to moderate workloads. Can handle hardwood, MDF, acrylic, and even light aluminum with proper settings.
- 3.0kW – 3.2kW: Popular in mid-range machines. Offers solid performance for most woodworking, signage, and general fabrication jobs.
- 3.5kW – 4.5kW: More torque and durability for continuous operation. Cuts hardwoods, plastics, and aluminum efficiently. Good for small production shops.
- 5.5kW – 6.0kW: Heavy-duty spindle power for demanding materials and deeper cuts. Suitable for larger jobs and moderate metalworking tasks.
- 7.5kW – 9.0kW: High-performance industrial use. Handles thick, dense materials and extended runtimes without overheating. Ideal for manufacturing environments.
When choosing spindle power, match it to your material, workload, and job complexity. Underpowered spindles limit what you can cut; overpowered ones raise costs without adding value unless you truly need the extra force.
What Are The Dangers Of Using 3-Axis CNC Routers?
- Moving Parts and Pinch Points: Exposed motors, gantries, and spindles can injure fingers or clothing if someone reaches into the machine while it’s running.
- High-Speed Cutting Tools: The spindle spins at thousands of RPM. Contact with the bit, while rotating or not, can cause severe injuries.
- Flying Debris: Wood, plastic, or metal chips can become projectiles during cutting. Bits can also snap and fly off. Eye protection is a must.
- Noise Exposure: CNC routers can be loud, especially in enclosed spaces or when cutting hard materials. Prolonged exposure can damage hearing.
- Dust and Fumes: Cutting wood, plastics, or composites generates fine dust and potentially toxic fumes. Without proper extraction, it can affect both machine and human health.
- Electrical Hazards: Improper wiring or damaged cables can cause an electric shock or fire. Always ensure proper grounding and use certified equipment.
- Fire Risk: Friction from cutting or a broken bit can ignite wood dust or flammable materials if the workspace isn’t well managed.
- Software or Input Errors: Incorrect G-code or setup can cause sudden, unpredictable movements, leading to crashes or damage to the machine and workpiece.
Used responsibly, 3-axis CNC routers are safe. But ignoring safety protocols can lead to serious accidents—so respect the machine and work smart.
What Maintenance Is Required For 3-Axis CNC Routers?
- Daily Maintenance
- Clean the Work Area: Remove chips, dust, and debris from the table, rails, and spindle.
- Inspect Tools and Bits: Check for dullness, wear, or cracks. Replace as needed.
- Lubricate Moving Parts: If the CNC router requires manual oiling, apply lubricant to rails and ball screws.
- Check Air Pressure (if applicable): For machines using pneumatic systems, verify pressure and filter condition.
- Weekly Maintenance
- Inspect Belts and Chains: Look for signs of wear, cracking, or looseness.
- Tighten Bolts and Screws: Vibration can cause hardware to loosen—check frame, gantry, and tool mounts.
- Check Spindle Runout: Spin the spindle and check for wobble or abnormal noise.
- Clean Linear Rails and Bearings: Wipe them down with a lint-free cloth and apply appropriate grease or oil.
- Monthly Maintenance
- Calibrate the Machine: Run test cuts or use a dial indicator to check for axis accuracy.
- Inspect Electrical Connections: Make sure cables, limit switches, and control boards are secure and undamaged.
- Drain Moisture from Air Compressors (if used): Prevent water buildup that can damage components.
- Annual or Long-Term Maintenance
- Replace Spindle Bearings (as needed): If the spindle is noisy or overheating, bearings may be worn.
- Update Software/Firmware: Check for updates from the machine or controller manufacturer.
- Deep Clean and Inspect: Take time to clean internal panels, control boxes, and check for wear on all mechanical systems.
- Important Notes
- Always follow the manufacturer’s maintenance schedule and use recommended lubricants and cleaning products.
- Log maintenance tasks to track wear, catch issues early, and stay organized.
Proper maintenance means fewer breakdowns, better cut quality, and a longer machine life. Stay consistent, and your 3-axis CNC router will keep delivering.
Get CNC Routing Solutions
If you have questions about our CNC routers, need a customized solution, or want to learn more about machine specifications, pricing, or delivery, we’re here to assist you every step of the way.
Simply fill out the contact form, email us, or reach out via phone. One of our knowledgeable representatives will get back to you promptly with the information you need. Partner with AccTek Group and take your manufacturing capabilities to the next level.